Projection Welding: Precision Bonding for Strong Connections
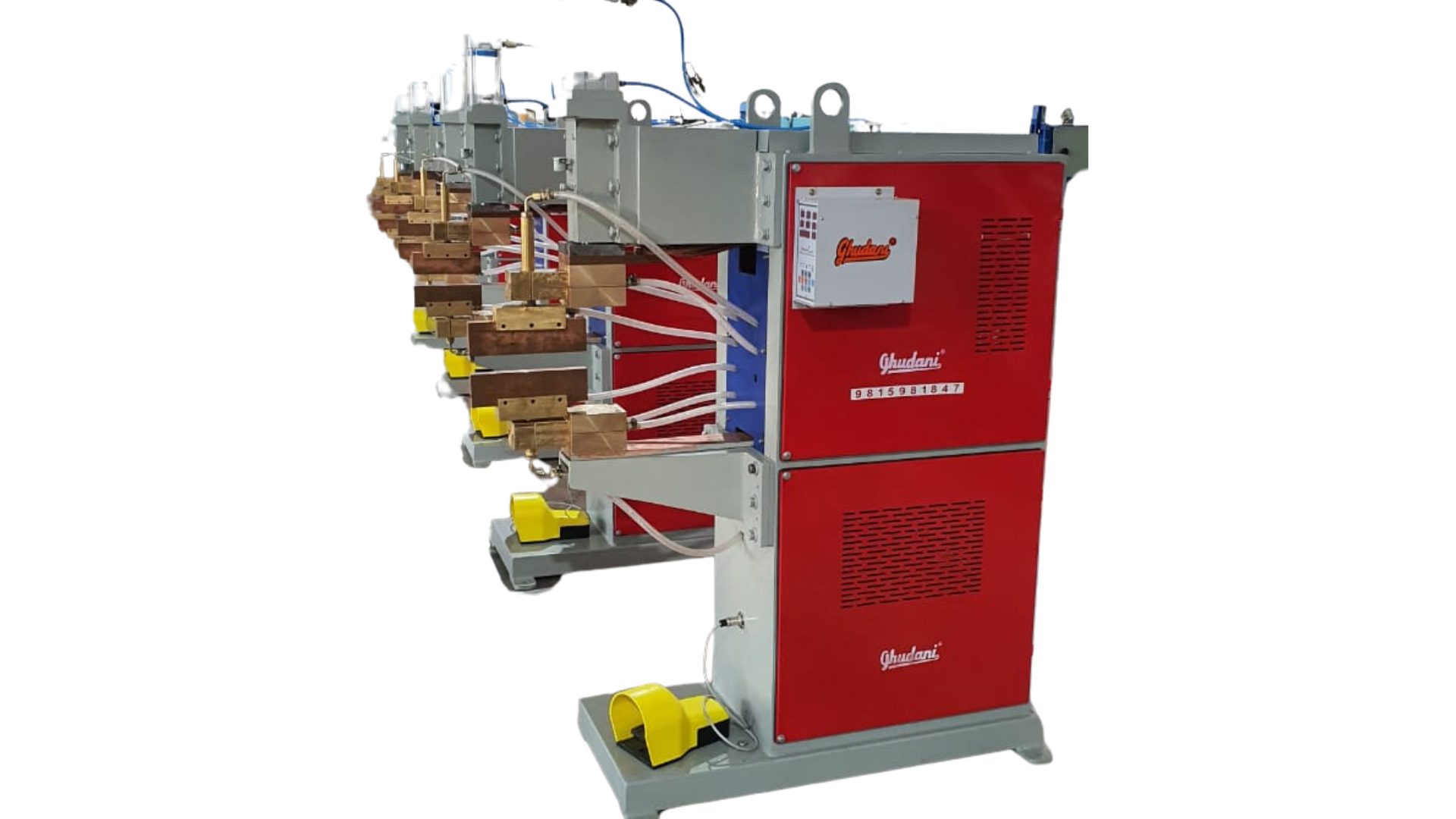
Welcome to our in-depth guide on projection welding, a sophisticated technique employed in the manufacturing industry for creating precise and robust welds. Whether you’re a seasoned professional or just delving into the world of welding processes, this page will take you through the essentials of projection welding, its mechanics, applications, and the advantages it brings to various industries.
The Projection Welding Process
- Preparation: As with other welding processes, proper preparation is crucial. The metal surfaces are cleaned and prepared to ensure optimal welding conditions.
- Fixturing: The metal components are securely fixtured, with the projections aligned for precise welding.
- Electrode Contact: Copper electrodes are brought into contact with the metal, concentrating pressure on the raised projections.
- Application of Current: A high electrical current is passed through the electrodes, creating resistance and generating heat at the projection points.
- Weld Formation: The heat melts the metal at the projections, creating a localized molten pool. As the metal cools and solidifies, the projections fuse, forming a strong and durable weld.
- Cooling: After the welding current is turned off, the welded joint is allowed to cool, finalizing the fusion process.